Rising Prices in Low-Cost Metros Creates Challenges in Site Selection
by Chris Schwinden, on Apr 13, 2023 8:30:00 AM
While there have been signs of cooling inflation in the last few months, understanding potential cost pressures continues to be top of mind for corporate location decision-makers. Markets that were considered competitive on cost yesterday are one mega-project announcement away from losing their cost advantage in terms of target wages, industrial rents, construction costs and affordable workforce housing. Other markets have seen costs steadily rise as more people and companies move there. Site Selection Group, a full-service location advisory, economic incentive and real estate services firm, monitors cost trends across the United States to see how changes in costs are influencing manufacturing site selection.
There is a myriad of ways to measure cost inflation across markets. One way is to look at cost trends, especially for industrial requirements, that either have a direct impact on a manufacturer’s cost structure, or are a good proxy measure for those factors. Those include:
- Real estate costs: measuring increases in industrial lease rates
- Labor costs: measuring overall wage growth and more specifically in manufacturing
- Housing: measuring overall cost pressures in a market
Markets with highest-cost inflation: Florida and Sunbelt markets (with one exception)
As a result, Site Selection Group reviewed one-, three-, and five-year cost-inflation data for these categories across all large and midsize markets in the United States (those with more than 500,000 in population). We then look at the average of those data points to point us toward which markets have experienced higher cost inflation:
The majority of these markets are in fast-growing Sunbelt states:
- Florida: Markets in the Sunshine State have seen significant cost inflation over the past five years.
- Southeast: North Carolina markets like Charlotte and Raleigh-Durham are joined by markets like Atlanta, Nashville and smaller markets like Knoxville. These markets have been tremendously active in manufacturing and logistics growth in recent years.
- Mountain West: It’s not surprising to see markets like Phoenix and Salt Lake City on this list —both have been favorite destinations for companies looking to serve the western U.S. or relocate from higher costs and less favorable operating conditions in California (Los Angeles and the Inland Empire are also on this list).
- Columbus, Ohio: While most of these markets are in the southern U.S., Columbus, Ohio is one geographic exception. But given recent major industrial announcements in the region, there are certainly cost pressures in that fast-growing Midwest hub.
Markets with lowest cost inflation: Midwest, Northeast and energy markets
On the other hand, Site Selection Group also looked at large and mid-size markets with lower overall cost growth. These are not necessarily markets with lower costs, just ones that have seen lower inflation over the past few years.
Those markets tend to be markets in the Midwest, like Minneapolis, Wisconsin or smaller markets scattered across the center of the country. The list also includes a handful of markets in the Northeast.
Curiously, the list also includes some major energy markets like Houston, Oklahoma City and Baton Rouge, Louisiana. Those markets tend to be heavily impacted by the ups and downs of global energy and commodity markets.
Markets with lower cost inflation and favorable demographics
There are many ways to measure whether a market is “good” for manufacturing investment. One simple way to look at the long-term viability of a market is to look at projected population growth. It’s a good, if simple, proxy data point for workforce alignment, but also for potential logistics considerations. As a result, the table below shows markets with lower cost growth, but with higher-than-average projected population growth.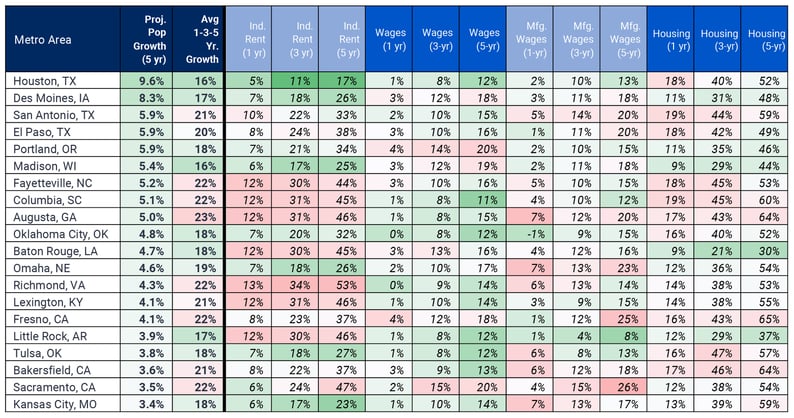
Site Selection Group summarizes these in a couple key categories:
- Alternatives to “overheating” Sunbelt markets: For example, San Antonio, Texas; Oklahoma City; Tulsa, Oklahoma; Little Rock and even El Paso, Texas, could be potential alternatives to markets with inflating costs. Fayetteville, North Carolina, while not a major manufacturing hub today, could be of increasing interest given its proximity to Raleigh-Durham. The same could be said for Columbia vs. Charlotte in North Carolina or Augusta vs. Atlanta in Georgia.
- Midwest alternatives: While they may not be as geographically well-centered to serve the U.S. population, markets like Des Moines, Iowa, and Omaha, Nebraska, could be of interest. Madison, Wisconsin, is not necessarily a “low-cost” option, but for biotech projects, its value proposition vs. Raleigh-Durham and eastern Pennsylvania could be improving.
- West Coast remains challenging: Quite simply, serving the West Coast is tough and companies will pay a premium to be there. While many companies choose to disregard California, it’s interesting to see how markets in the Central Valley like Sacramento, Fresno and Bakersfield may see their value proposition to manufacturers improve compared to Phoenix and Salt Lake City.
Build a good cost model, refine it and test your assumptions
The industrial market is as dynamic as it’s ever been. Southern markets that hung their hats on cost advantages are seeing those advantages dissipate. Other markets that have historically the highest cost may see that gap shrink. Every manufacturing project is different in terms of workforce, logistics, real estate requirements and tax structure. Now more than ever, it’s critically important to build a robust comparative cost analysis in any site selection exercise. And perhaps even more importantly, refine that model and test future cost assumptions as the project progresses. No one can see the future, but past cost inflation data shows where some markets may be headed.